Firebolt420
Member
I have a '74 MX 16 and the time has come to tear into the transom. I am in the planning and gathering stage so there is some general confusion for me going on. I store my boat in a friends shop that is not heated so glass work on the boat will happen at my place of employment over Thanksgiving and Christmas breaks allowing me access to a full machine shop and cnc machines while everyone is off for the breaks
My confusion is over the best process for doing the re-transom. I have searched and read so much info that it has become overwhelming. I plan on using poly resin from US Composites and I'm not sure which resin would work best for me and how much I should purchase to assure that I wont need for more during the lay-up. I assume I should use the 435 poly resin and 2 gal of it, but we know where assumptions can get us. The next part of this confusion is what fiber cloth to use and how much of that to use. Cost is a factor, I know it will be around $500ish for materials but I would like to keep it down when possible.
I plan to use a bit of Redstrat's genious design for the transom and elimination of
the splashwell using this plywood http://www.menards.com/main/buildin...-8-marine-grade-plywood/p-1485663-c-13332.htm
and make my adjustments in this way.
The fuel tank will nest between kickers that the "shelves" will attach to. I realize the 19 gal tank will be a lot of weight when full but it will only be full when we are going on river camping trips and the weight will be balanced by personnel and gear in the bow. Any other time it will be around 1/4 full so that will washout itself.
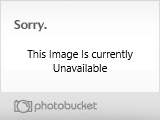
So this is where I am at, let the info flow

My confusion is over the best process for doing the re-transom. I have searched and read so much info that it has become overwhelming. I plan on using poly resin from US Composites and I'm not sure which resin would work best for me and how much I should purchase to assure that I wont need for more during the lay-up. I assume I should use the 435 poly resin and 2 gal of it, but we know where assumptions can get us. The next part of this confusion is what fiber cloth to use and how much of that to use. Cost is a factor, I know it will be around $500ish for materials but I would like to keep it down when possible.
I plan to use a bit of Redstrat's genious design for the transom and elimination of
the splashwell using this plywood http://www.menards.com/main/buildin...-8-marine-grade-plywood/p-1485663-c-13332.htm
and make my adjustments in this way.
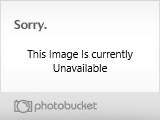
The fuel tank will nest between kickers that the "shelves" will attach to. I realize the 19 gal tank will be a lot of weight when full but it will only be full when we are going on river camping trips and the weight will be balanced by personnel and gear in the bow. Any other time it will be around 1/4 full so that will washout itself.
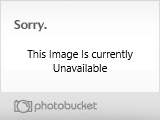
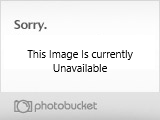
