Diplomat82
Well-known member
I started with the port side stringer since that is the easy side.
Since I'm working with epoxy I decided to for go the mat and just apply three layers of 1700 biaxial cloth. This stuff is so hard to wet out and work with but I think it will be very strong and waterproof when done.
I also decided to redesign the motor mount support. I'm going to incorporate it into the stringer and triple up the 3/4" plywood in the engine bay. This way I can thru bolt an aluminum angle right to the stringer. This will also give me a little more room to work around the motor.
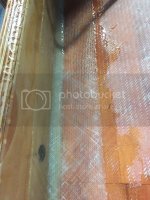
Peanut butter fillet and one layer of biaxial cloth
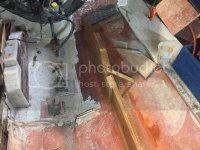
Peanut butter fillet and One layer of biaxial cloth
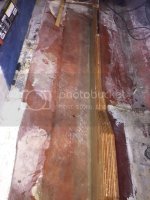
Two layers of biaxial cloth
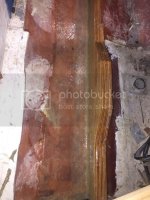
Two layers of 1700 biaxial cloth added.
Well I figured out that I'm not the best at applying epoxy and cloth. This 1700 is so hard to work with but should be very strong when finished. This is three layers and the stringer is fully encapsulated now. I had to piece in a few little sections so I need to clean it up a bit:
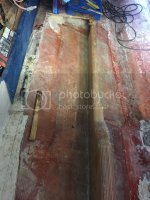
Since I'm working with epoxy I decided to for go the mat and just apply three layers of 1700 biaxial cloth. This stuff is so hard to wet out and work with but I think it will be very strong and waterproof when done.
I also decided to redesign the motor mount support. I'm going to incorporate it into the stringer and triple up the 3/4" plywood in the engine bay. This way I can thru bolt an aluminum angle right to the stringer. This will also give me a little more room to work around the motor.
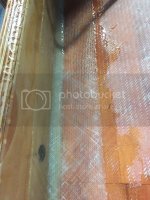
Peanut butter fillet and one layer of biaxial cloth
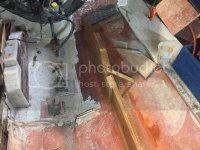
Peanut butter fillet and One layer of biaxial cloth
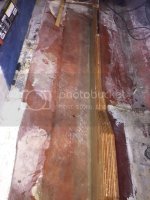
Two layers of biaxial cloth
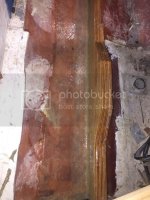
Two layers of 1700 biaxial cloth added.
Well I figured out that I'm not the best at applying epoxy and cloth. This 1700 is so hard to work with but should be very strong when finished. This is three layers and the stringer is fully encapsulated now. I had to piece in a few little sections so I need to clean it up a bit:
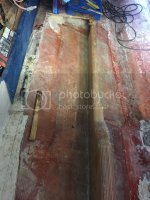